Dryers
Our Products
Chemical Process Equipment : Dryers
Tray Dryers
Drying ovens are fabricated in double walled M.S, S.S. Sheet construction. This is mounted on a rigid steel frame work. Glass wool, mineral wool, Rock wool, is used for insulation which is placed in the gap of two layers.
Steam radiator or heaters are used and the air is passed through it which are totally enclosed. This hot air is then circulated in here by me of a fan fitted on the side of the oven and driven by a suitable electric motor.
The unit is also provided with air inlet, air filter adjustable air outlet, self locking insulated door etc, A control panel is provided in front of the oven which consists of , Digital Temperature Controller, P.T 100 Sensor, Ameters, Push button on-off operation, indicating lamps, earthing bolt etc. duly interconnected suitably.
The ovens are available in a vast range i.e to accommodate the trays from 12 to 192 Nos., The trays are made S.S or Aluminum sheets. M.S. or S.S. wheeled trolley of standard size will be provided.
M.S. Unit is painted from outside with synthetic epoxy paint. If required ovens can also be supplied in flame proof construction.
S.S.unit is buffed for inside mirror & out side mat finish
Available in – 6, 12, 24, 48, 96, 192, Tray
Capacity Model (STD/ GMP)
Type: – Electrical / Steam Heating arrangement
Trays :- In S.S.304, S.S.316, S.S.316L, Aluminum, P.P.etc
Rotary Dryers.
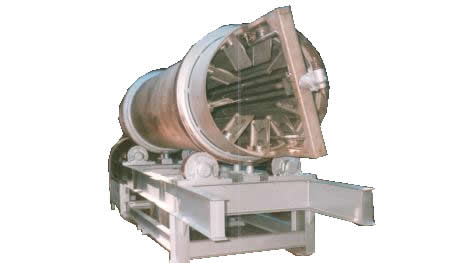
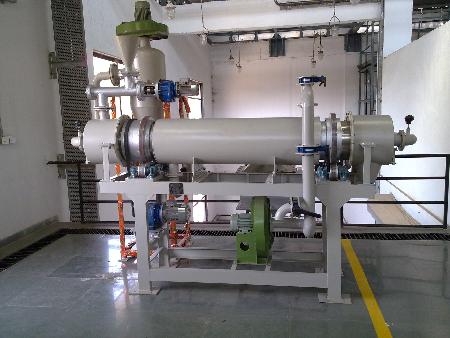
Alternatively, the gas stream may consist of air or another (sometimes inert) gas that is preheated. When the gas stream is preheated by some me where burner combustion gases do not enter the dryer, the dryer known as an indirect-heated type. Often, indirect heated dryers are used when product contamination is a concern.
Available Capacity : 100 Kg/hr. to 1000 Kg/hr.
Available M.O. : M.S. , S.S. 304, S.S. 316, S.S. 316 L etc.
Vacuum Tray Dryers

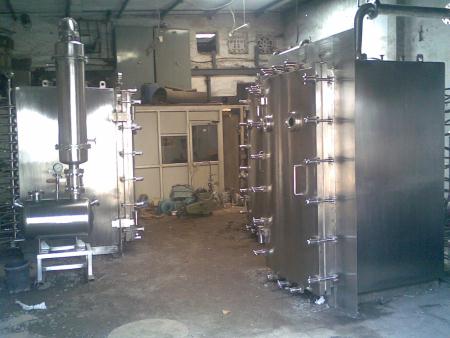
Used mainly for drying of high grade, temperature and oxygen sensitive products highly suitable for drying hygroscopic substances, which are dried to very low residual moisture, content level. Frequently vacuum drying cabinets are the sole possibility for drying lumpy, glutinous products or products of low pompality.
Vacuum tray dryer is the most commonly used batch dryer. They are box-shaped and loaded and unloaded via a door ( two doors on the larger models). Inside are several heating plates is water, steam or thermal oil. The distance between the heating plates is determined primarily by the surface loading.
The preheating phase is very important I order that the drying curve & the foaming of the product is identical throughout the cabinet. During the main drying phase the vacuum is in the range of 40 to 80 mbar abs & in the final drying phase vacuums of only few mbar abs are reached.
The dimensioning of the vacuum system is an important factor in the design of drying cabinet systems.
Available capacity :- Dryer range from 4 trays to 96 trays
M.O – M.S, S.S.304, S.S.316, S.S.316L , Hallar Coated etc.
Heating Media:-Electrical Heater/Steam Coil
Electric & Steam coil type
Rotary Vacuum Dryer
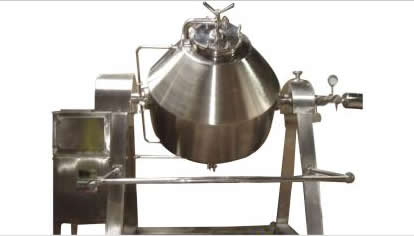
The Rotary Vacuum Dryers offered by us are a clean, simple and effective way to dry wet cakes, wet powders and slurries. These are used where either a solvent is to be recovered or the drying is to be carried out at relatively low temperatures for heat sensitive material. We manufacture our range using high grade material that includes C.S, SS 304 and SS 316. Available in different capacities, ranging from 50 liters to 16000 liters, these find application in industries related to dyes, pigments, agrochemicals, polymers, metal powders, herbal products, pharmaceuticals, food products and speciality chemicals.
Capacity : 0.5m3 to 10.0m3
MOC:- M.S. S.S.304, S.S. 316 SS 316L Material Jacketed or Limpeted type .
Applications : Chemicals, Pharmaceuticals, Food Products, Resins, Dyestuffs.
Rotary Vacuum Paddle Dryer
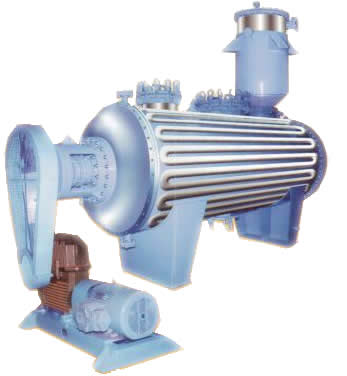
Rotary Vacuum Paddle Dryer is a jacketed cindrical vessel with a large diameter hollow shaft. Attached to the shaft are hollow paddles provided with specially designed scraper blades, which scrape the entire internal surface of the dryer and continuously move and rotate the material thereby precluding the possibility of material remaining in contact with hot surfaces for protracted periods of time.
The jacket and hollow shaft with paddles can be heated with hot water, steam or any other thermal fluid capable of providing a larger indirect heat trfer area. Cooling can be also be done by cold water, brine or any other refrigerant through the jacket and hollow shaft.
Limpet coil can be provided in lieu of jacket, if liquid heating medium is used. Hard facing of shaft provided in way of gland packing areas of trunnions. Arrangements for nitrogen purging provided. Bag cleaning arrangement with pulsation by nitrogen jet injector provided.
Heavy duty trunnions and bearings support the hollow shaft and the drive is provided by me of a motor through reduction gears chain and sprocket.
Provision has also been made to insert four breaker bars inside the dryer shell for particle size reduction.
In special cases, stationery scraper blade can be provided to scrape the rotating agitator, for highly sticky material.
Silent features:
Ideal for temperature sensitive materials.
Almost 100% recovery of solvents. Low energy consumption.
CAP:- 10 LTRS TO 30000 LTRS
MOC:- MS,SS 304,SS316,SS316
Screw Dryers an
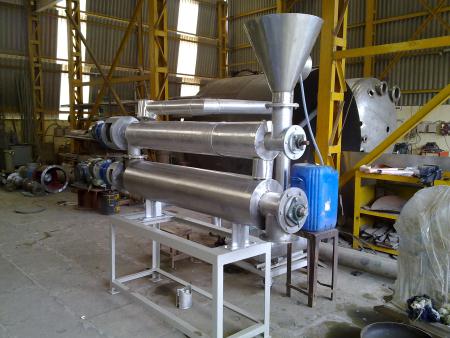
Lamina Dryer an
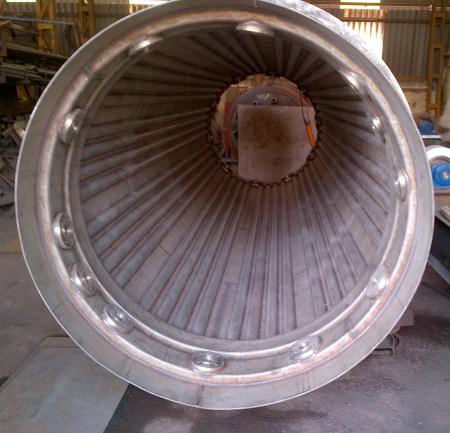
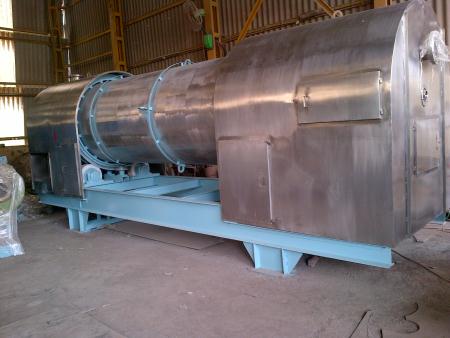
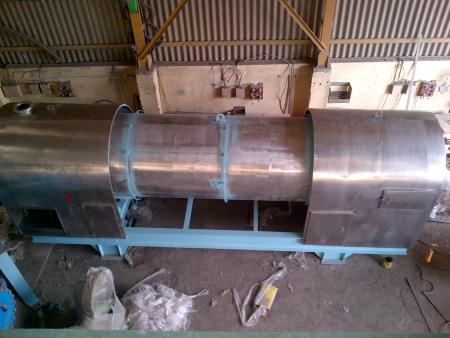